To accurately calculate your plastic product’s manufacturing cost, you’ll need to analyze three core components: direct materials, labor, and overhead expenses. Start by determining your direct material costs through a detailed bill of materials (BOM), including raw plastics and packaging supplies. Next, calculate labor costs by multiplying production hours by wage rates, including both direct workers and supervisors. Then, assess overhead expenses like utilities, equipment depreciation, and maintenance costs, dividing them by your production volume. Breaking down these components systematically will help you establish precise unit costs and develop competitive pricing strategies.
Key Takeaways
- Calculate direct material costs by determining the amount of plastic resin, additives, and packaging materials needed per unit through a BOM.
- Determine direct labor costs by multiplying production hours by wage rates, including operator and supervisor time per production run.
- Compute manufacturing overhead by adding utilities, equipment depreciation, and maintenance costs, then allocate based on production volume.
- Track equipment costs through initial investment, depreciation schedule, and ongoing maintenance expenses spread across projected production units.
- Monitor quality control expenses within overhead calculations to account for testing, inspection, and potential waste reduction measures.
Understanding Plastic Manufacturing Costs
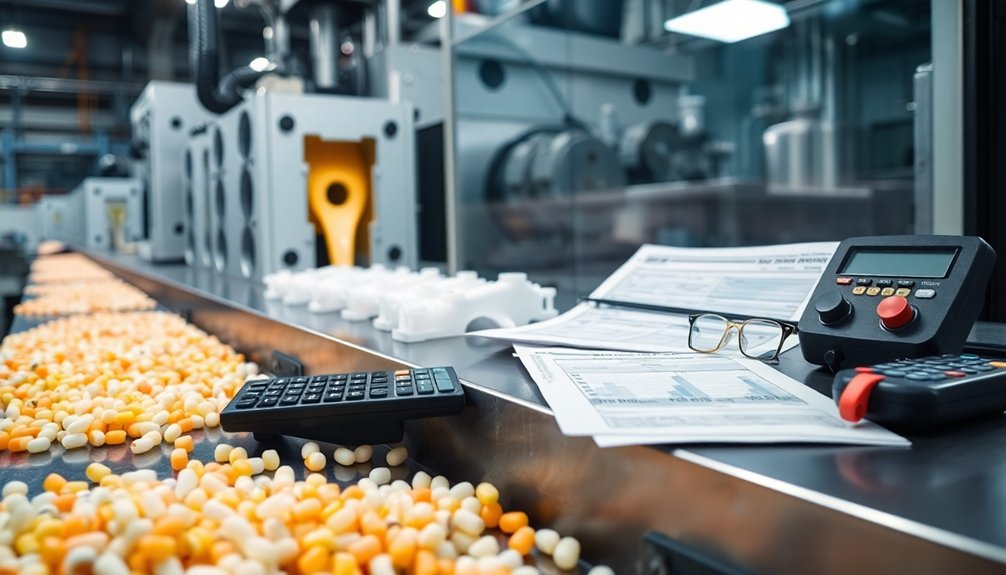
When calculating the manufacturing cost of plastic products, you’ll need to take into account three primary components: labor costs, overhead expenses, and equipment investments. Each element plays a significant role in determining your final product cost and pricing strategy.
Effective tracking of direct material costs is essential for establishing accurate raw material expenses throughout production. You’ll start by calculating your labor costs by dividing total wages by units produced. For instance, if your monthly labor costs are $1,000 and you’re producing 500 units, your per-unit labor cost will be $2. This calculation must account for both hourly workers and salaried supervisors separately.
Your overhead costs will include utilities, depreciation, and indirect expenses. You’ll need to allocate these based on labor or machine hours. For example, if you’ve got an overhead rate of $50 per labor hour and 100 hours of production time, you’re looking at $5,000 in overhead costs.
Equipment and machinery costs form the third component, incorporating initial investment, depreciation, and ongoing maintenance. You’ll need to spread these costs over your equipment’s expected lifespan and factor in regular maintenance expenses.
Together, these three components will give you an accurate total manufacturing cost.

Direct Materials Cost Analysis
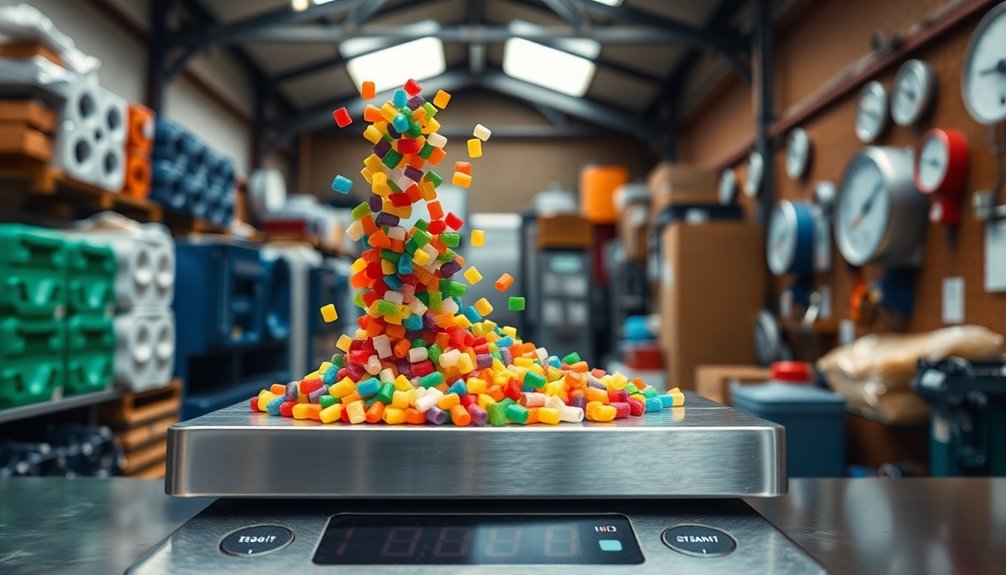
Three key components make up direct materials cost analysis in plastic manufacturing: raw materials, additives, and packaging supplies.
You’ll need to identify and calculate costs for each polymer resin, processing aid, and packaging material that goes into your finished product.
To calculate your direct materials cost, you’ll want to start by reviewing your bill of materials (BOM) and determining the exact quantities needed for each component. The beginning inventory plus purchases, minus the ending inventory, will give you the actual materials cost. You can then multiply these quantities by their respective costs to establish your total direct materials expense per unit.
You’ll find that proper classification of direct materials is vital for accurate cost allocation and inventory valuation. Make sure you’re including all components that can be directly traced to the production of your finished goods.
Your direct materials costs will typically represent the largest portion of your total manufacturing expenses, so accuracy is essential. Use your purchase orders and inventory records to verify current material prices and maintain precise documentation of all components.
These calculations will help you develop effective pricing strategies and make informed decisions about your production processes. Through careful analysis, you’ll better understand your product’s true cost structure.
Labor Cost Components
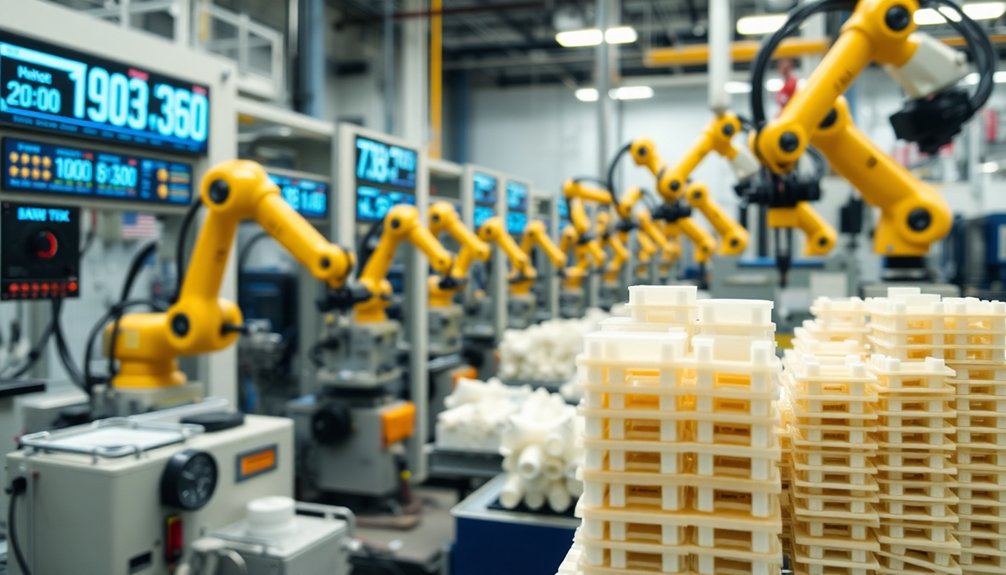
Understanding labor costs in plastic manufacturing requires careful analysis of both direct and indirect workforce expenses. You’ll need to track hours spent on production tasks and multiply them by appropriate wage rates, including overtime and benefits calculations.
Direct labor costs involve your production line workers who are hands-on with the plastic manufacturing process. You’ll want to monitor their hours, skill levels, and productivity rates to determine accurate per-unit costs. Employee training investments can significantly improve productivity and reduce costly errors.
Don’t forget to factor in shift premiums and overtime rates that may affect your calculations.
Your indirect labor expenses include support staff like maintenance technicians, quality control personnel, and supervisors. These costs, combined with facility overhead, need to be distributed across your production volume using predetermined rates or activity-based costing methods.
The geographic location of your facility will greatly impact your labor rates, as will the level of automation in your processes.
You’ll need to calculate your total labor cost per unit by dividing the combined direct and indirect labor expenses by your production volume.
Consider implementing efficient workforce management systems and training programs to optimize your labor costs while maintaining product quality and consistency.
Manufacturing Overhead Assessment
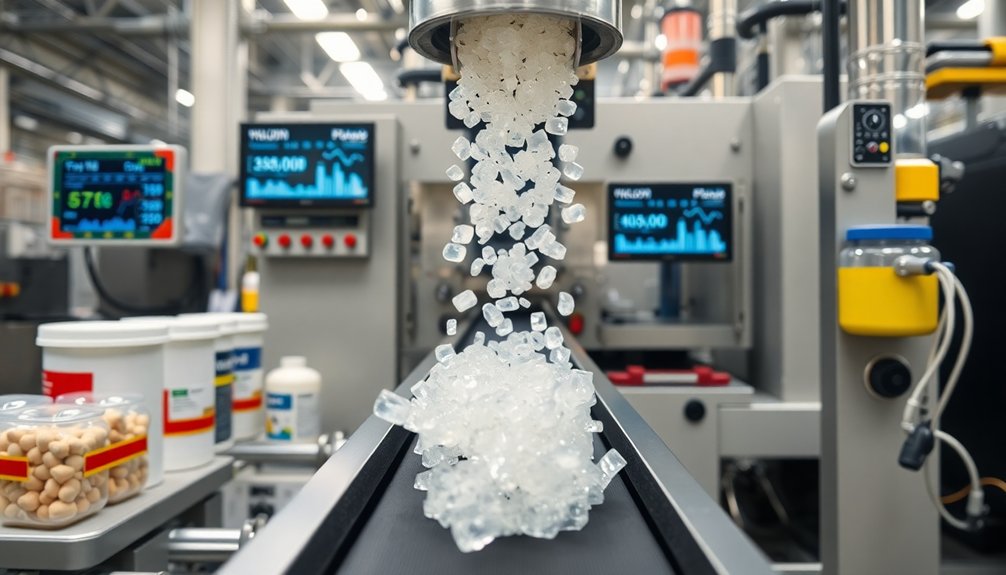
Beyond direct labor costs, manufacturing overhead represents a significant portion of your plastic product’s total cost structure.
You’ll need to identify all indirect costs that support your production process, including utilities, equipment depreciation, and maintenance expenses.
Start by listing every overhead cost category that affects your plastic manufacturing operation. You’ll want to gather data from utility bills, maintenance records, insurance policies, and supervisor payroll information to create a thorough cost picture.
Quality control expenses help ensure product consistency and reduce waste, making them an essential part of your overhead calculations.
To calculate your overhead rate, you’ll need to choose an appropriate allocation base for your plastic production facility. Machine hours often work well for plastic manufacturing since it’s typically equipment-intensive.
Divide your total overhead costs by your selected allocation base to determine the rate.
You can improve accuracy by implementing activity-based costing, which links specific overhead costs to particular production activities. This method helps you understand how different plastic products consume resources differently, leading to more precise cost calculations.
Make sure to regularly review and update your overhead calculations as costs and production processes change.
You’ll maintain better cost control by monitoring these indirect expenses closely.

Total Cost Calculation Methods
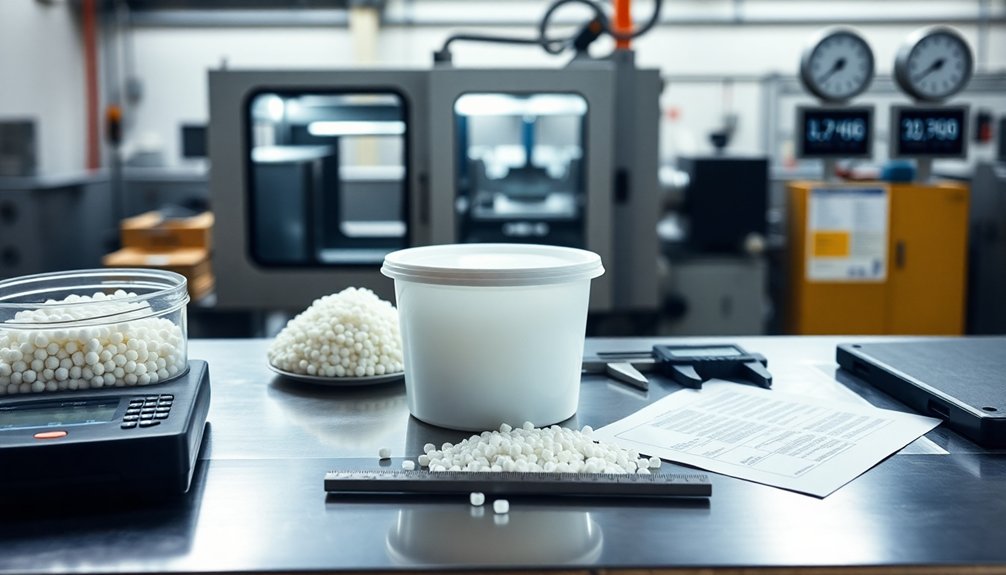
Calculating total manufacturing costs requires a systematic approach that combines direct materials, direct labor, and overhead expenses.
You’ll need to track each component separately before bringing them together for your final calculation using the formula: Total Manufacturing Cost = Direct Materials + Direct Labor + Manufacturing Overhead.
Start by determining your direct material costs by multiplying the quantity of each raw material by its unit price. For plastic products, this includes the base plastic material, additives, and packaging materials.
Next, calculate your direct labor costs by multiplying the total production hours by the applicable wage rates, including any related payroll taxes.
For manufacturing overhead, you’ll need to add up all indirect costs such as utilities, equipment depreciation, and production supervision salaries. Using a predetermined overhead rate or activity-based costing method will help you allocate these costs accurately to your plastic products. Automated tracking systems can significantly reduce calculation errors and improve data accuracy.
Once you’ve gathered all these components, combine them to determine your total manufacturing cost.
You should review these calculations regularly to identify cost-saving opportunities and maintain accurate pricing strategies.
Cost Per Unit Determination
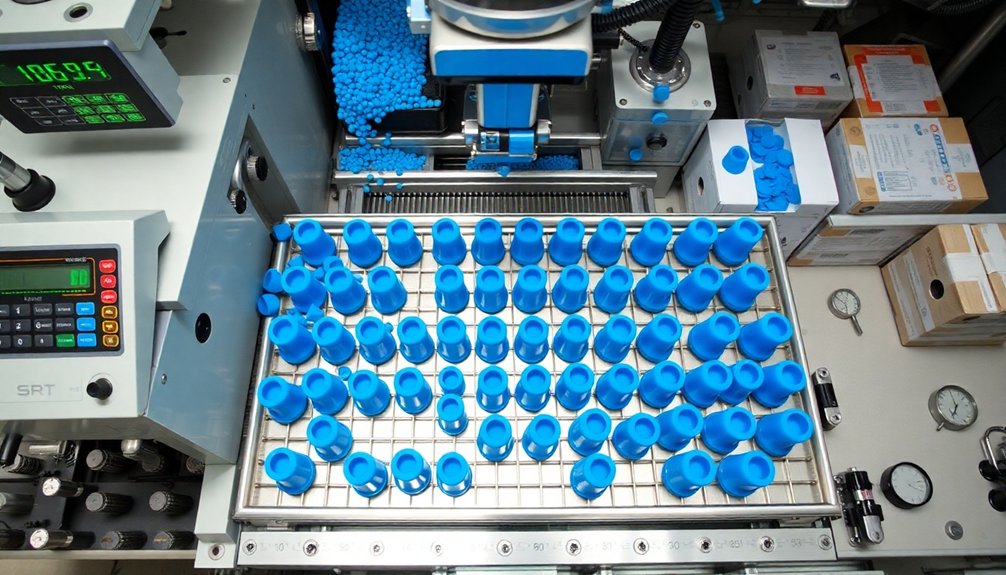
The cost per unit serves as an important metric for plastic manufacturers to price products competitively and maintain profitability. To determine this vital figure, you’ll need to gather extensive data about your total manufacturing costs and production volume during a specific period.
- Raw material costs, including plastic resin quality and market prices
- Direct labor expenses for operating machinery and handling materials
- Manufacturing overhead costs, such as equipment maintenance and energy
- Production capacity variations and efficiency rates
- Environmental compliance costs and sustainable material considerations
Begin by calculating your total manufacturing cost by adding direct materials, labor, and overhead expenses. Next, track the exact number of units produced during your chosen time frame, ensuring accurate production data collection. Accurate tracking of these components helps identify cost-saving opportunities and maintain quality standards.
You can then divide the total manufacturing cost by the number of units to determine your cost per unit.
Your cost per unit calculation isn’t static – it requires regular updates to reflect market changes and operational adjustments. Monitor factors like oil prices, supply chain dynamics, and production efficiency to maintain accurate cost assessments.
This information will help you make informed decisions about pricing strategies and profitability targets.
Cost Monitoring and Adjustment
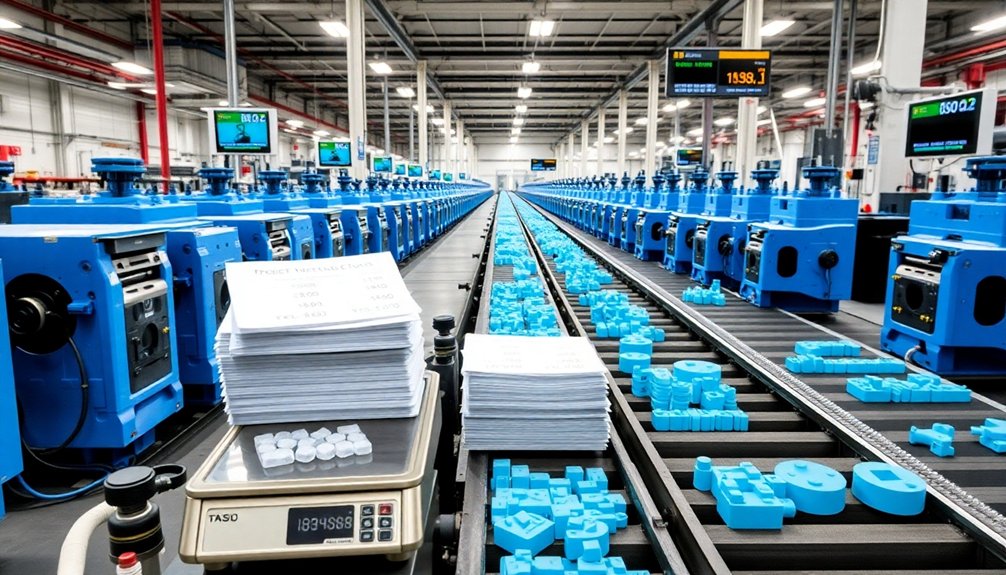
Once you’ve established your initial cost per unit, maintaining an effective monitoring system becomes your next key focus. You’ll need to track various cost components and make adjustments to maintain profitability while staying competitive.
Start by implementing real-time monitoring of your direct material and labor costs, using detailed breakdowns for each production run. You’ll want to utilize process costing for bulk production while maintaining job order costing for customized products. Regular supply chain audits can help identify potential disruptions that may impact your material costs and availability.
Cost Component | Monitoring Strategy |
---|---|
Direct Materials | Track quantities against design specs |
Labor Costs | Monitor hours and efficiency rates |
Overhead | Calculate equipment depreciation and utilities |
Supply Chain | Implement just-in-time inventory systems |
Technology | Use cost estimation software |
Compare your costs regularly against industry benchmarks to identify areas needing improvement. You’ll need to adjust your processes based on these findings, whether it’s optimizing your supply chain or implementing lean manufacturing principles.
Don’t forget to leverage modern technology for cost tracking and analysis. You should utilize dedicated cost estimation software to enhance your monitoring capabilities and guarantee you’re capturing all relevant data points accurately.

Frequently Asked Questions
How Do Seasonal Changes in Plastic Production Affect Manufacturing Costs?
Seasonal changes considerably impact your plastic production costs through demand fluctuations and raw material price variations.
You’ll notice higher costs during peak seasons like holidays and farming periods, when increased demand drives up production expenses and material prices.
During low seasons, you’ll experience reduced costs due to oversupply, but you’ll need to manage inventory carefully.
Your production efficiency will also vary as you adjust output levels to match seasonal demand patterns.
What Impact Does Product Color Selection Have on Overall Manufacturing Expenses?
Your product’s color selection greatly impacts your manufacturing expenses through raw material and production costs.
You’ll pay more for organic pigments than inorganic ones, while higher quality pigments increase costs but provide better coloration and durability.
You can manage these expenses by implementing color reduction strategies, such as minimizing the number of colors in your product line and optimizing production processes.
This approach helps balance cost efficiency with brand consistency.
Does Packaging Type Influence the Final Manufacturing Cost Calculation?
Yes, packaging type greatly influences your final manufacturing cost calculations through several key factors.
You’ll need to take into account the material selection, which affects both durability and shipping expenses, as well as design complexity that impacts labor and production costs.
Additionally, your packaging volume requirements will determine economies of scale, while specific shipping needs, such as protective features for fragile items, can considerably increase your overall manufacturing expenses.
How Do Different Mold Cooling Methods Affect the Total Production Cost?
Just as water and air flow differently through channels, your choice of mold cooling method greatly impacts your total production costs.
You’ll find water cooling offers faster cycle times but requires higher maintenance and equipment costs due to complex piping systems and sealing requirements.
In contrast, air cooling reduces maintenance expenses and works better above 100°C, though it may extend cycle times.
Your cooling method selection affects both direct operational costs and long-term equipment expenses.
What Role Does Warehouse Temperature Control Play in Plastic Manufacturing Costs?
Warehouse temperature control directly impacts your plastic manufacturing costs through both material preservation and energy expenses.
You’ll need to maintain specific temperatures (60-75°F) to prevent material degradation, which helps avoid waste and quality issues that could increase your production costs.
Your temperature-controlled storage expenses will affect overhead calculations and total manufacturing costs, but you’ll typically save money through reduced material waste and extended shelf life of your raw materials.